CHOOSE PDP FOR ELECTRICAL SERVICES
- 24 hour emergency call outs
- Free estimates
- Rewiring and additions
- Part P certification
- Additional sockets
- Full electrical installations
- Safety electrical inspections
- Security alarms & CCTV
- Lighting
- Security Lighting
- Lighting design
- Portable Appliance Testing
- Exterior lighting
- PAT Testing
- Domestic installations
- Commercial installations
- All work guaranteed
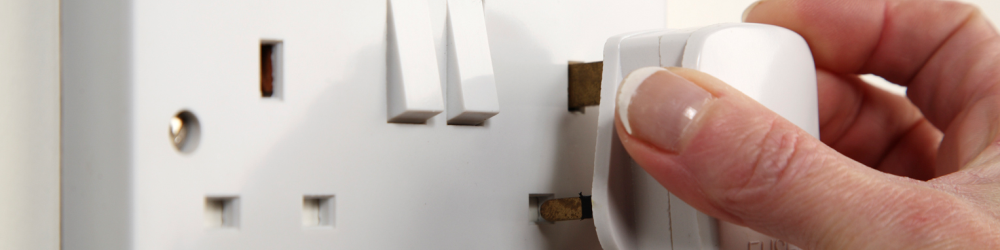
Portable Appliance Testing (PAT)
PDP Services specialise in Portable Appliance Testing (PAT Testing) for businesses in and around the Sussex area. Our team of electricians carry all the necessary equipment and are able to deal with all aspects of Portable Appliance Testing to ensure that your business complies with the latest electrical laws and regulations.
Contact us for a free estimate.
What is Portable Appliance Testing?
“In Service Inspection and Testing of Electrical Equipment”, “Portable Appliance Testing”, “PAT Testing” or simply “PAT” is a means by which companies can comply with the Electricity at Work Regulations and other such legislation covering safety in the workplace.
If you own a business that employs staff you must ensure that the electrical appliances are safe to use. Equally if you work for an employer they have a legal responsibility to ensure the appliances you use are safe.
PAT Testing is a very important procedure which is legally required in order to comply with four different regulations. It’s increasingly required to meet insurance requirements. The only way to fully comply with the regulations is to employ a registered company (such as PDP Services) to carry out the inspection and testing.
PDP’s PAT Testing Service
We send fully trained professionals to carry out your PAT Testing using the latest hi-tech computerised equipment. Once we’ve conducted the testing we then issue full results complete with a detailed asset list.
We carry out FREE minor repairs as we go to avoid down time. We also have the ability to carry out in-line testing which means vital equipment like computer servers etc. do not have to be turned off during testing. Each item will have a label attached indicating whether an appliance has passed or failed.
Our PAT Testing Service includes:
- FREE minor repairs
- Labelling of each item
- In line testing
- Full test results
- Detailed asset list
Do I need to have my items PAT tested?
There are around 1000 electrical accidents in the workplace each year, involving some 30 deaths. The “Health and Safety at Work act” (1974) puts a duty of care upon both employer and employee to ensure the safety of all persons using the work premises.
Landlords and letting agents are also duty bound to ensure any appliances supplied as part of a tenancy are safe.
“The Provision and Use of Work Equipment Regulations” 1998 requires every employer to ensure that equipment is suitable for the use for which it is provided (reg 4 (1)) and only used for work for which it is suitable (Reg 4(3)). It requires every employer to ensure equipment is maintained in good order (reg 5) and inspected as necessary to ensure it is maintained in a safe condition (reg 6). Therefore there is a requirement for regular inspection and testing of all electrical equipment in all work situations.
It should be noted that the safety and proper functioning of certain portable appliances depends upon the integrity of the buildings fixed electrical installation. It is equally important to establish a system for the inspection and testing of the fixed installation as well as the portable equipment used within a building. (Requirements for fixed installations are given in BS 7671 and guidance can be found in IEE guidance note 3.)
Frequency of in-service testing
The frequency of testing depends on a number of factors, including:
- Type of premises Environment where equipment is used
- The user of the equipment, equipment type and construction
The IEE publishes guidelines for the initial testing frequency of appliances according to the appliance type and premises where it is to be used. However, the most appropriate schedule can only be arrived at after repeated in-service tests. Equipment which is found to be failing regularly will need to be tested on a more frequent basis to ensure its safe operation. Also the opposite may be found to be the case. PDP can help you establish the best schedule to comply with the appropriate regulations. Many insurers now stipulate annual testing as a requirement for their cover and have been known to not pay out in the event of an accident being caused by untested equipment.
Portable Appliance Testing Laws
The responsibilities for the safety of persons at work have been prescribed at great length in much legislation in recent years.
Of specific relevance to Electrical Maintenance are: –
- The Health & Safety at Work Act 1974. This puts the duty of care upon both the employer and the employee to ensure the safety of all persons using the work premises. This includes the self-employed.
- The Management of Health & Safety at Work Regulations 1999
- The Electricity at Work Regulations 1989
- The Provision and Use of Work Equipment Regulations 1998
- The Workplace (Health, Safety and Welfare) Regulations 1992
The Management of Health & Safety at Work Regulations 1999 states:
“Every employer shall make suitable and sufficient assessment of:
(a) The risks to the health and safety of his employees to which they are exposed whilst at work, and
(b) The risks to ensure the health and safety of persons not in his employment arising out of or inconnection with the conduct by him or his undertaking.”
The Provision and Use of Work Equipment Regulations 1998 states:
“Every employer shall ensure that work equipment is maintained in an efficient state, in efficient working order and in good repair.”
The PUWER 1998 covers most risks that can result from using work equipment. With respect to risks from electricity, compliance with the Electricity at Work Regulations 1989 is likely to achieve compliance with the PUWER 1998.
PUWER 1998 only applies to work equipment used by workers at work. This includes all work equipment (fixed, transportable or portable) connected to a source of electrical energy. PUWER does not apply to fixed installations in a building. The electrical safety of these installations is dealt with only by, the Electricity at Work Regulations.
The Electricity at Work Regulations 1989 states:
“As may be necessary to prevent danger, all systems shall be maintained so as to prevent, so far as reasonably practicable, such danger.”
“‘System’ means an electrical system in which all the electrical equipment is, or may be, electrically connected to a common source of electrical energy and includes such source and such equpment”
“‘Electrical Equipment’ includes anything used, intended to be used or installed for use, to generate, provide, transmit, transform, rectify, convert, conduct, distribute, control, store, measure or use electrical energy.”
Scope of the legislation
It is clear that the combination of the HSW Act 1974, the PUWER 1998 and the EAW Regulations 1989 apply to all electrical equipment used in, or associated with, places of work. The scope extends from distribution systems down to the smallest piece of electrical equipment. It is clear that there is a requirement to inspect and test all types of electrical equipment in all work situations.
If you need PAT Testing for your business call PDP today on 01444 480444.
We are based in Burgess Hill and we have engineers available in the surrounding areas including Haywards Heath, Bolnore Village, Cuckfield, Balcombe, Lindfield, Wivelsfield, Chailey, Ditchling, Hassocks, Hurstpierpoint, Brighton, Hove, Shoreham, Portslade and Worthing.